A mixing elbow is an external part on a diesel engine that combines the sea water (used for cooling the engine) with the combustion exhaust gases. The mixture is usually directed downwards into the bilge through a large diameter wet exhaust pipe leading to a thru-hull exiting the boat at the stern. An anti-siphon loop is somewhere in the exit hose to prevent water from coming in from the thru-hull in a following sea. Because of the harsh environment of hot gases and saltwater, mixing elbows have a lifetime of around 6-10 years and engine manufacturers suggest inspection every 3 years. OEM mixing elbows are typically made of steel and last a lot shorter time than ones made of 316 stainless steel.
The mixing elbow on Apropos was a stainless steel custom-made part that was 20 years old with 2850 engine hours. Space constraints in the engine bay required a custom part with specific bends and angles to clear the cabinetry. I periodically inspected the welds which are typically what fails first. It probably lasted so long because the boat has been moored in fresh water for 18 of the past 20 years. I also run the engine hard on my way back to the dock which helps clean out the exhaust elbow. Removing it was easy–3 bolts attaching it to the engine, the fresh water input hose, and the wet exhaust output hose. The 3″ diameter exhaust hose was only 30″ long, so I decided to slice the ends to make it easier to remove from the exhaust elbow. I also cut the other end which was attached to a fitting on the exhaust muffler. I bought a new 34″ hose (Trident-Flex) at Fisheries Supply for half price since it was a remnant, and used an angle grinder with a cutting disc to cut it to the correct length.
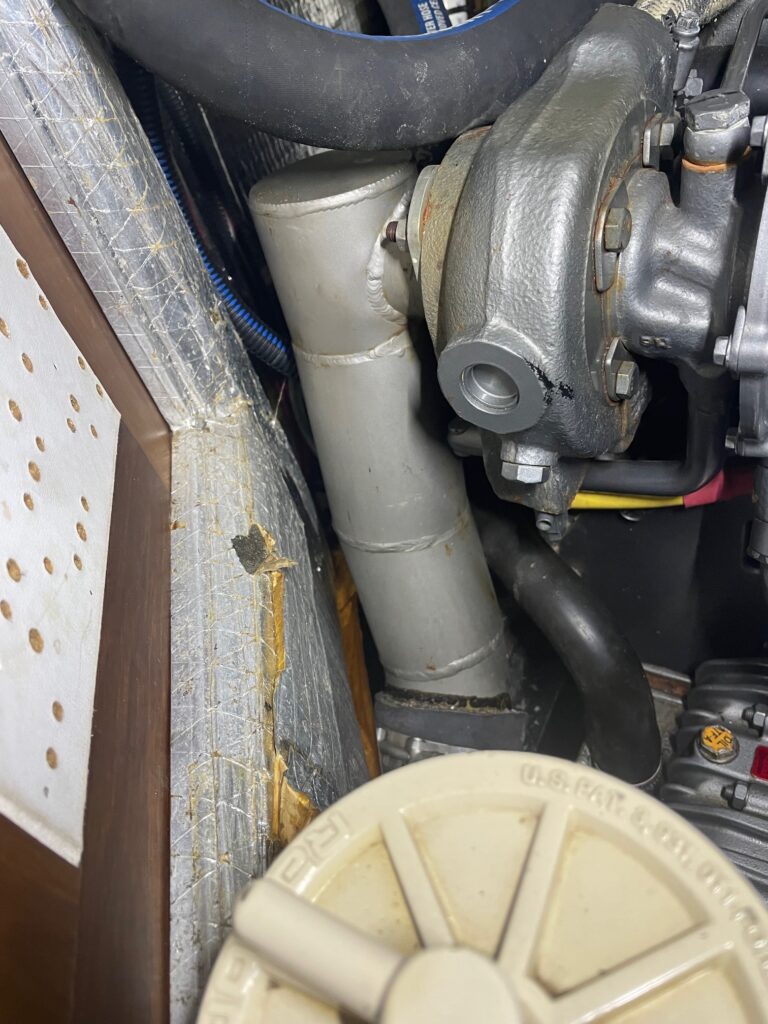
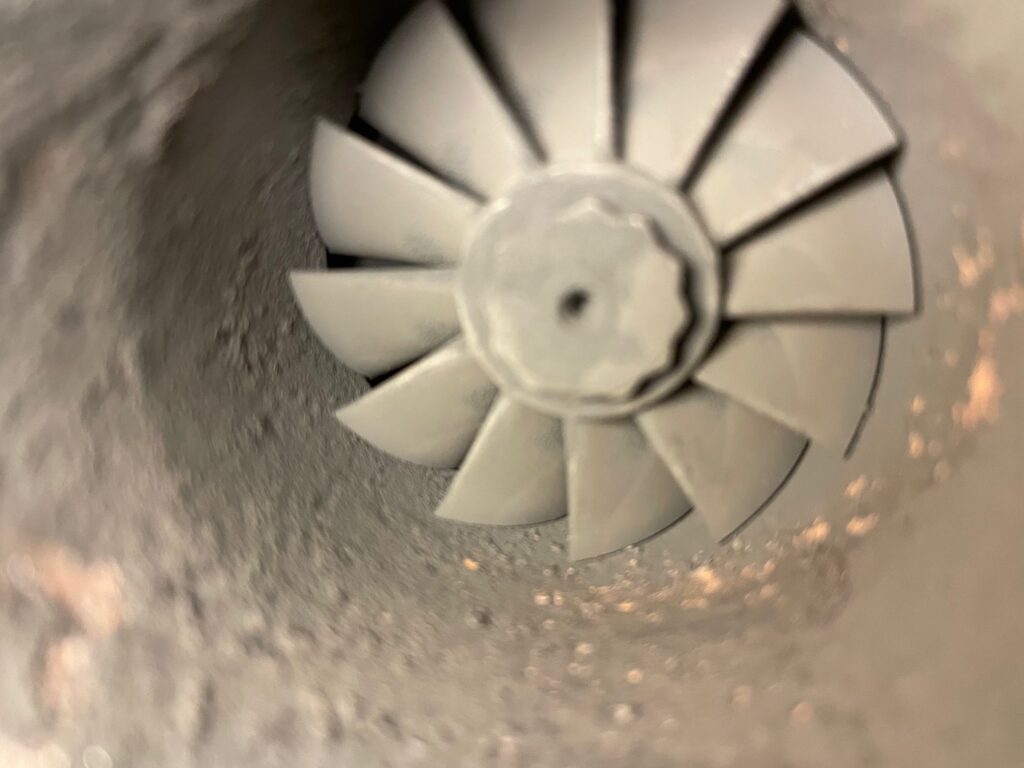
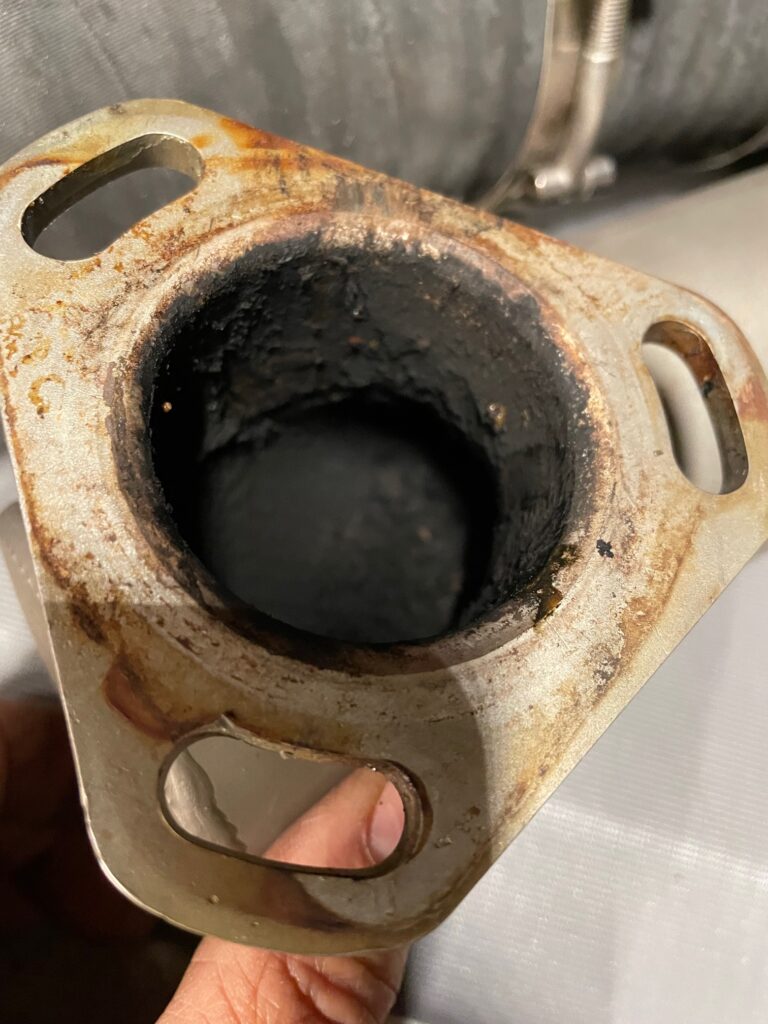
I delivered the old part to National Marine Exhaust (Marysville, WA) for them to duplicate. A week later I had the new exhaust elbow. It’s made of 316L (low carbon) stainless steel. Something they did different was to run the inner pipe (for exhaust) all the way to the output end. In the original part, the inner pipe only went 6″ from the sea water inlet. I guess the new design would cool the hot exhaust gasses more before they are combined with the sea water at the beginning of the wet exhaust hose.
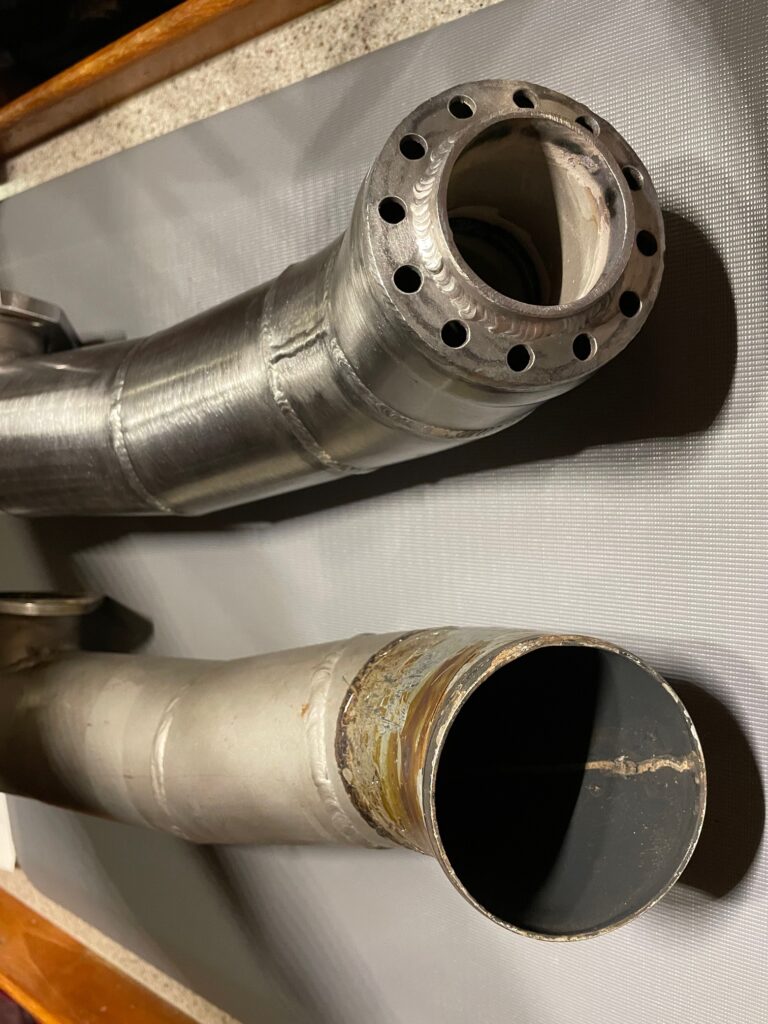
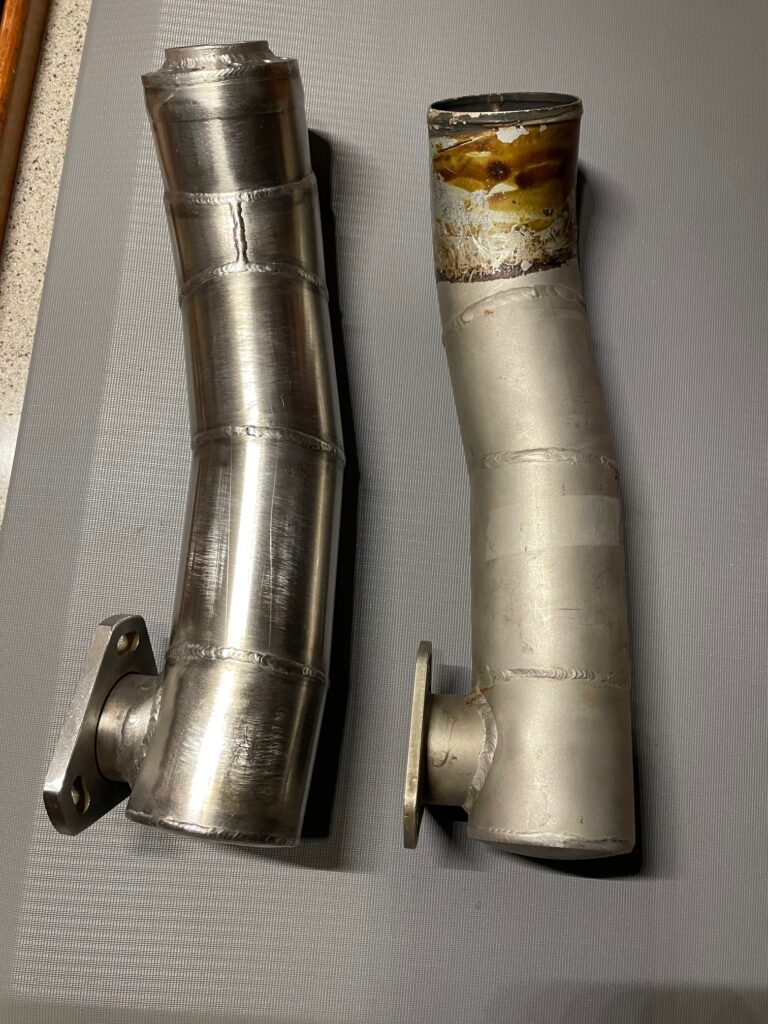
Installing the mixing elbow and new wet exhaust hose was a little harder than removal. I chose a 30 deg F day so the boat inside temperature was in the 40s. The first thing I did was to use bronze wool on the surface where the elbow attaches to the engine exhaust manifold to make it smooth for the fiber gasket. The Trident-Flex is anything but flexible, especially when cold. I warmed it up a bit using a heat gun, but it was still a struggle trying to bend it while fitting the ends onto the muffler and exhaust elbow. After a few attempts, I decided it would be easier to attach the hose first to the muffler using the 2 heavy duty ss hose clamps, then attach the other end of the hose to the mixing elbow, then attach the mixing elbow to the engine while bending the hose (the hard part). Eventually it all went back together. The final step was to run the engine to check for any leaks.
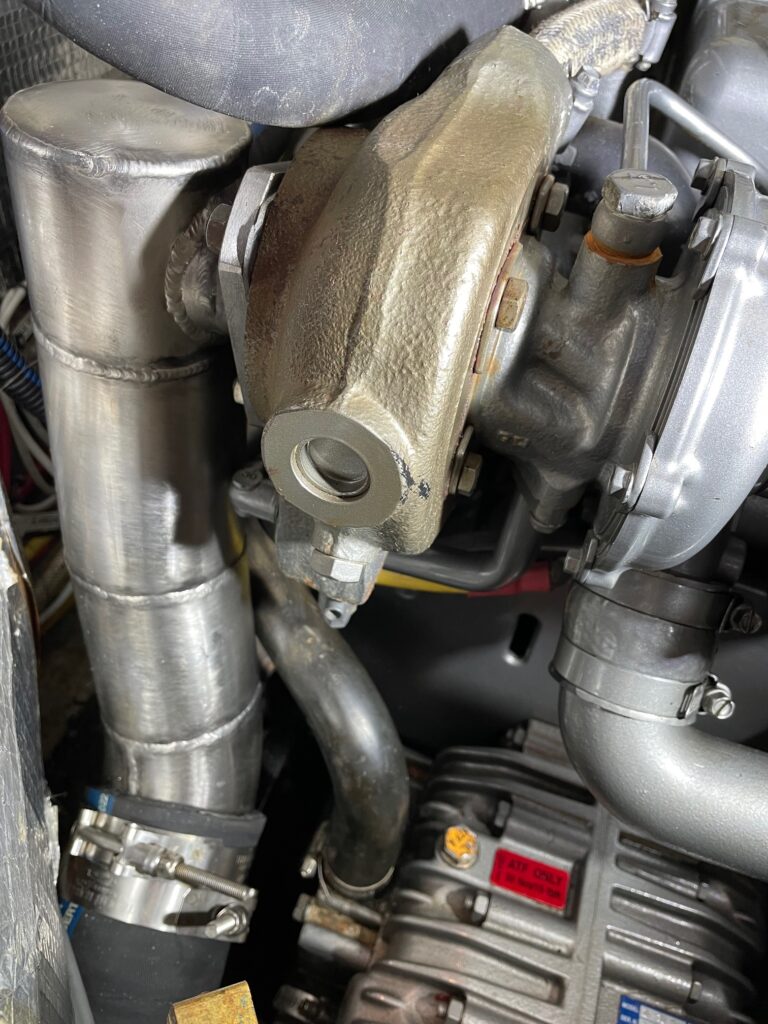