After owning a boat for a long time (16 years in my case), I find myself repeating certain tasks. A lot of this cannot be avoided (bottom paint, hull polishing, oil changes, etc). But there are some things I do because I like the outcome–like keeping the teak brightwork nice, keeping the bronze ports and pedestal shiny–so I’m always looking for ways to increase the time between when something needs to be re-done. For example, I switched from using varnish to using Awlwood Clear on all the brightwork and can now go 2-3 years between refresher coats.
I discovered another product that helps save time by keeping polished metal from oxidation–ProtectaClear by Everbrite. I mostly use this for interior bronze and brass, but am also experimenting with a few exterior items.
Interior Bronze and Brass
Apropos has a lot of interior bronze and brass. Today when you buy a brass fixture, it usually comes with a coating to protect it from oxidation (it also likely to be only brass coated vs solid brass). When Apropos was built in 1982, all of the bronze/brass was very high quality and didn’t have any protection layer to keep it from oxidizing. The sink faucet and hand pump in the head are the originals, made of heavy bronze. Being in a wet area, they tend to oxidize quickly so I would typically hand polish them once or twice a year to make them shiny again. But this takes an hour and only lasts a few weeks before becoming dull and eventually green again. So I recently gave them an extra good polishing using a dremel tool and polishing compound, then applied 4 layers of ProtectaClear. In the galley, the sink faucet is not original, so it has a protective film (lacquer?) that keeps it shiny, but next to it, the hand pump, water tank vents, and water maker port are all bare bronze, so I polished and coated them as well. I also polished and coated 2 oil brass oil lamps that are gimbal-mounted to bulkheads. I’ll use these items as test cases to see how well they look after a year, then decide if I want to do more interior bronze/brass items. Another nice thing about ProtectaClear is that is bonds to itself and only takes minutes to apply with a foam brush. Re-coats can be done after an hour.
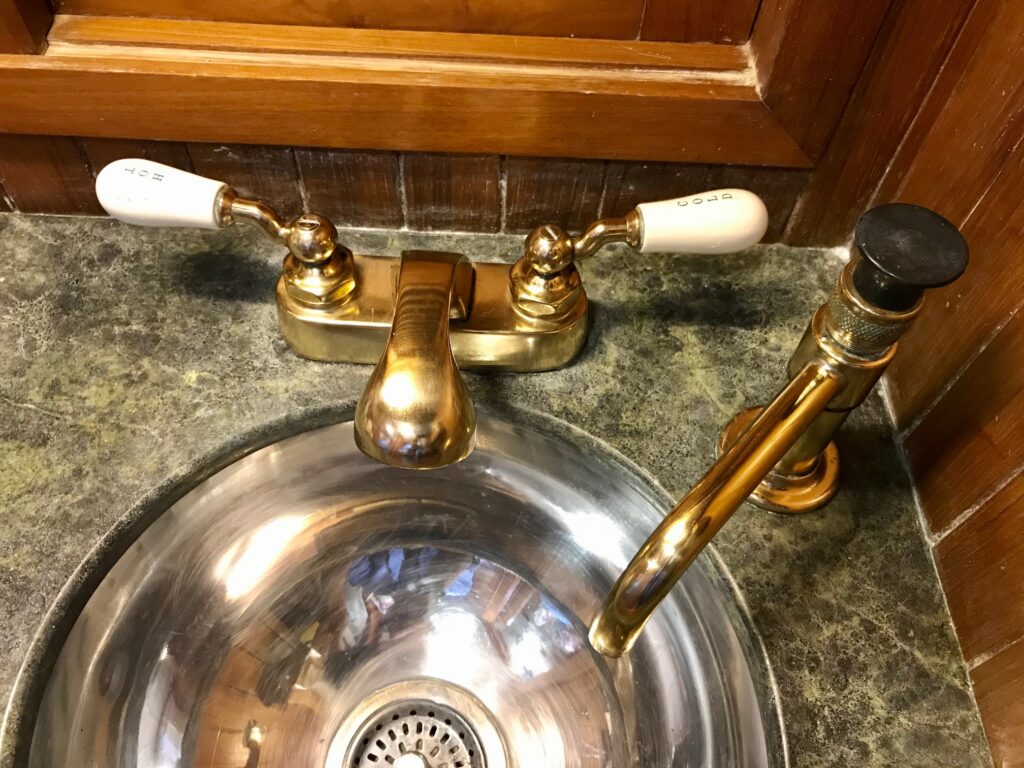
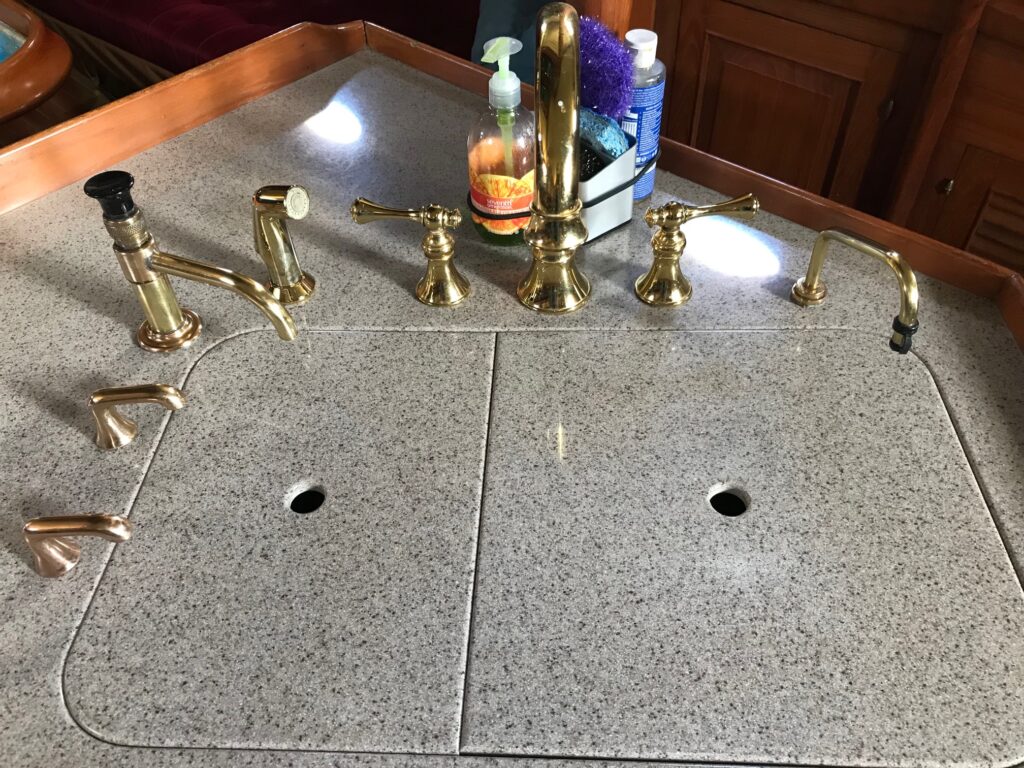
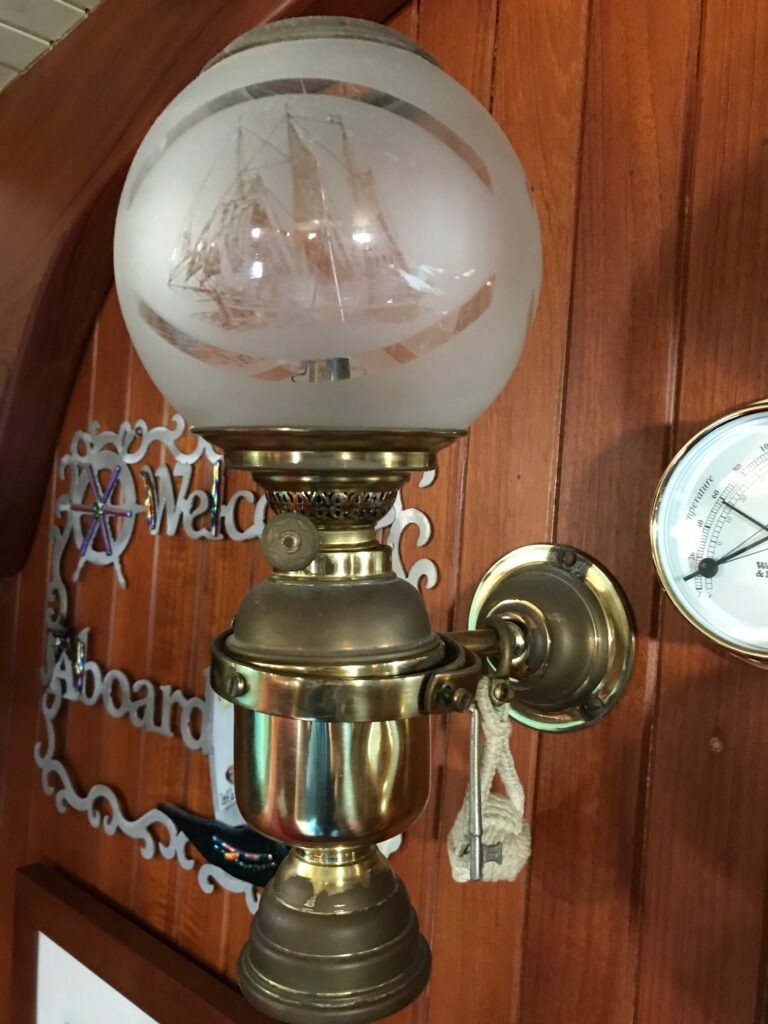
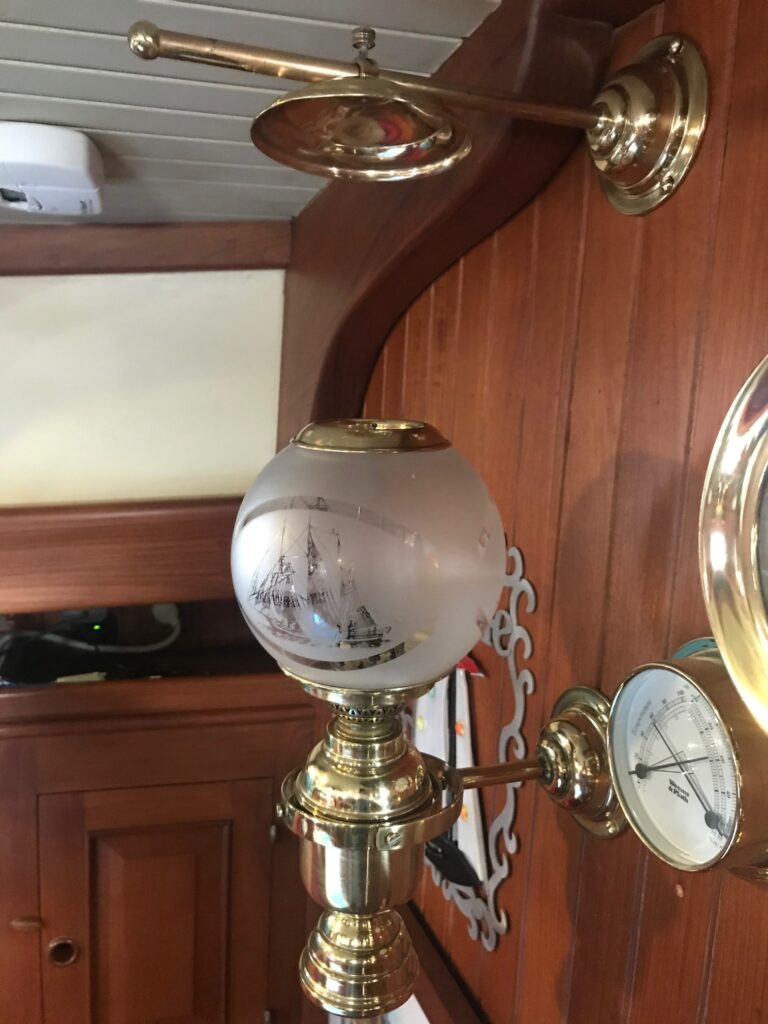
Exterior Bronze and Brass
The main exterior items I used the ProtectaClear on are small brass hardware latches and hinges found on all my deck boxes, helm seat, and cabin hatch doors. These are also protected by canvas covers so I think the coating will hold up well. As an experiment, I also polished and coated 3 bronze deck prism rings and the bowsprit star. These are all exposed to the elements (rain, salt water, UV) and the deck prisms are also stepped on. I applied 4 coats and will see how they look after a season.
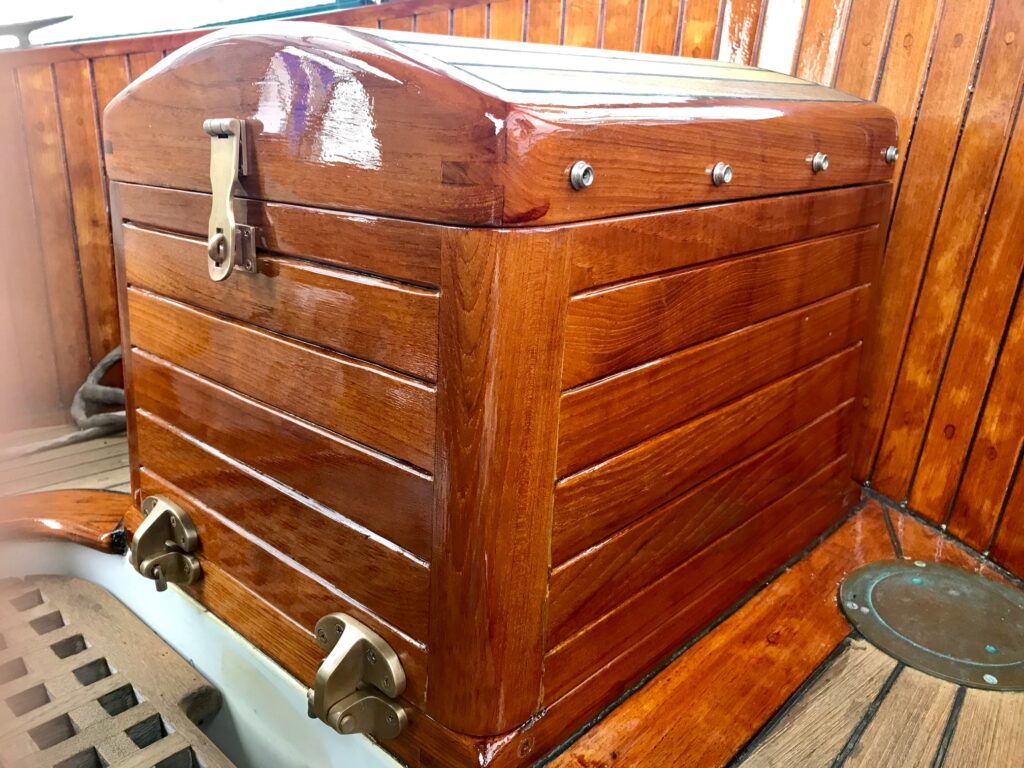
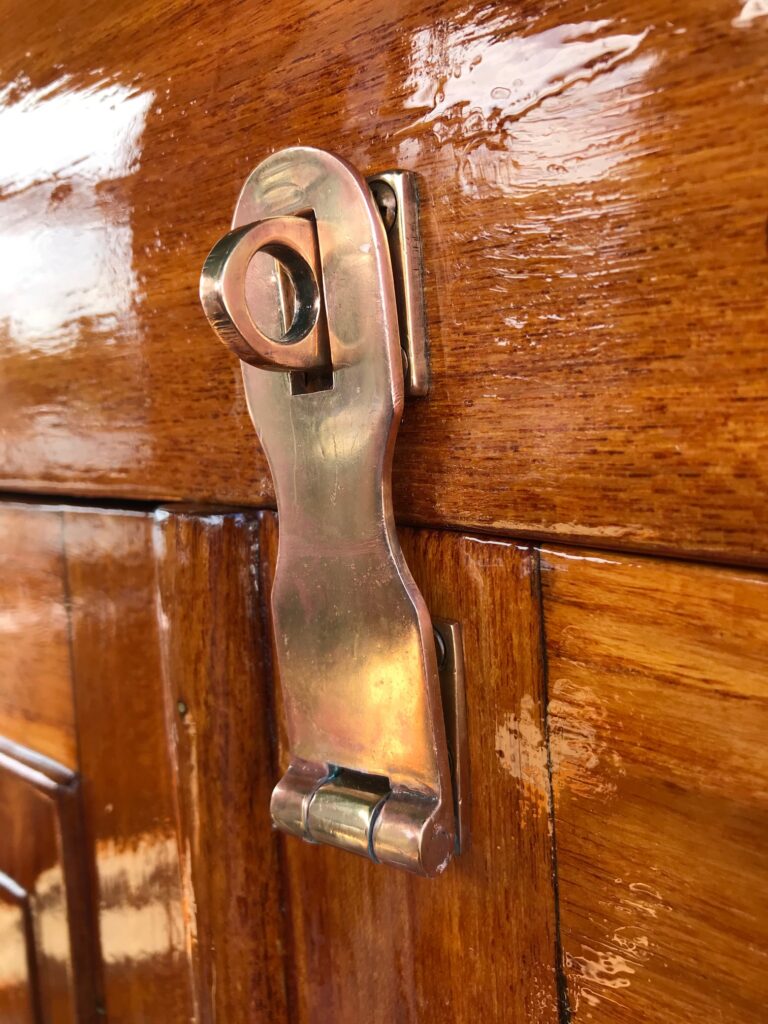
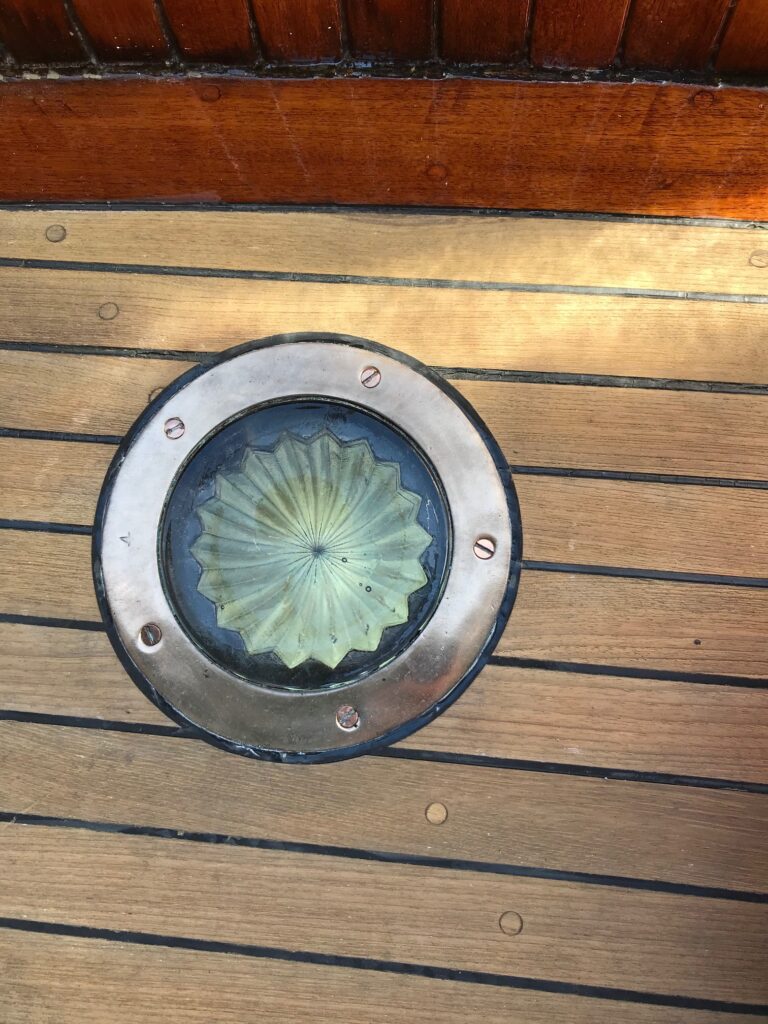